It doesn’t take a lot of investigation to determine that audiophile equipment prices can get very expensive. In our beloved industry, we see floorstanding speakers, audiophile subwoofers, power amps, stereo preamps, and beyond that cost well into the five-figure range—and sometimes into six-figure territory. And some manufacturers make claims about their processes and technologies that seem a little too far-fetched to believe. With 35 years of experience in the world of advanced, computer-driven manufacturing, I’m able to take a look at some of the concepts, keywords, and maybe even tropes of the audiophile world to see which ones carry the most weight.
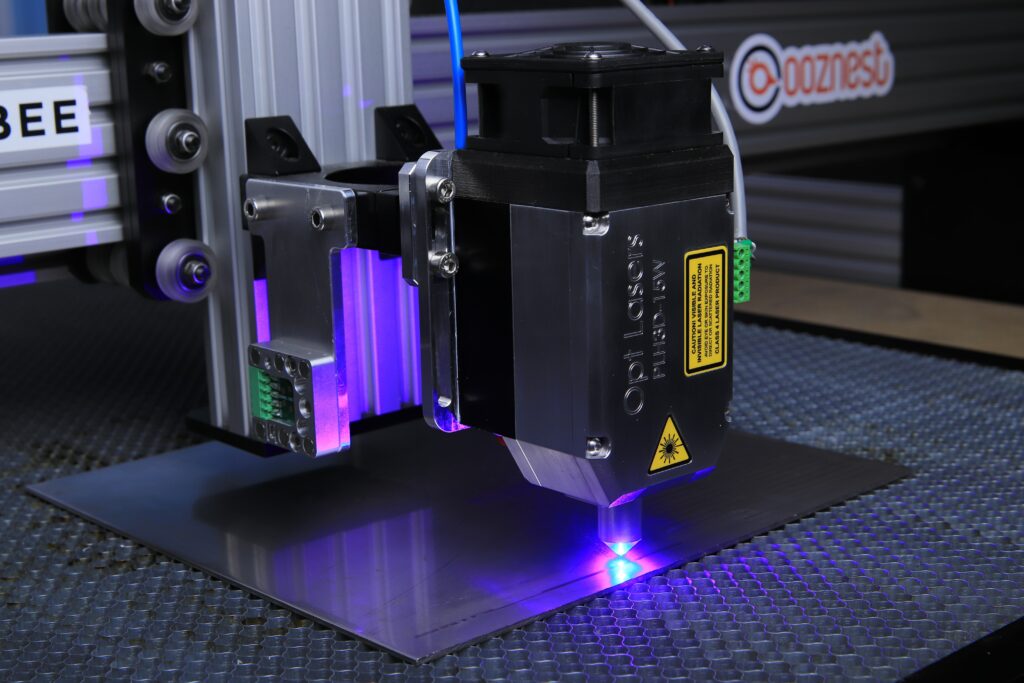
Made From Solid (Aluminum) Billets
The aluminum used to make faceplates on amps, preamps, DACs, and similar audiophile components is almost always machined by process. In the old days (25 years ago or longer), machining was as much art as science. Actual human machinists with decades of experience used their knowledge to basically hand-make dimensionally correct parts. These guys were artisans in a world without computers to guide them. Today, machining is commonly done by CNC, or Computer Numerical Controlled, equipment. Once the part drawing is loaded into the CNC machine, the operator presses start, and the machine takes over, often in a very impressive fashion. (I’m being very simplistic here because the operator needs to be highly skilled.) What makes CNC machining so magnificent are the close tolerances that can be held by today’s instruments. Regardless of the audio application (component faceplates, best audiophile speaker components, whatever), close-tolerance machining delivers a better part.
The CNC-machining operation involves cutting, grinding, drilling, and tapping—basically any process to remove metal from a big block. In the audio industry, the most common metal is aluminum; the type of aluminum will vary depending on what mechanical properties are required. For machining applications, the aluminum upon which the machining operation takes place is called a billet. Essentially a block of aluminum is loaded into the CNC machine, and the cutting process begins. But aluminum is not the only material that can be machined in this manner. Even the wood used for the best audiophile speaker housings can be cut using the CNC process.
What makes machining more expensive than almost any other manufacturing process commonly used in audio equipment is a set of three cost centers: scrap rate, labor burden, and secondary process. First, all machining produces scrap. It’s not uncommon to have almost as much scrap in terms of weight as the part itself weighs. The cost is derived from the weight of the entire billet, not just the finished part. So the total amount of scrap, plus the finished part itself, is figured into the final cost. Some could make the argument that the scrap can be resold and/or reused, but it is rarely (if ever) a profit center. Overall, the less scrap produced, the lower the cost of the part going into your audio component.
Secondly, labor burden translates to the cost of running the machine. Each shop will use its own formula to derive its own machine rates. Labor burden is the hourly cost of operating the machine. It can include the cost of the equipment itself, operator salary, utilities, building/overhead costs, and any other parameters the machine shop chooses to include. Each machine used in the making of the final part has a labor burden assigned.
Finally, secondary processes add to the cost. After the part is machined, it must be deburred.Machining leaves sharp edges and burrs that may cut or injure someone handling the part. No one wants to turn their amp on and inadvertently draw blood from a needlessly rough edge. So deburring is a necessary step and is commonly done by a process called Vibratory Deburring. There are a variety of ways to clean up the edges on a machined part, and this is only one of them.
Next in the audiophile machining process comes finishing. This is the process where the part is made to look pleasing. It may include applying a brushed finish, like in the case of many audio faceplates. A part may also be plated or painted, which in both cases involves a chemical finish being applied to the part.
All of these cost centers add to the bottom line, which is why machining is the most expensive manufacturing process used for making metal parts used in audio applications. It is one major reason why audiophile equipment is so expensive.
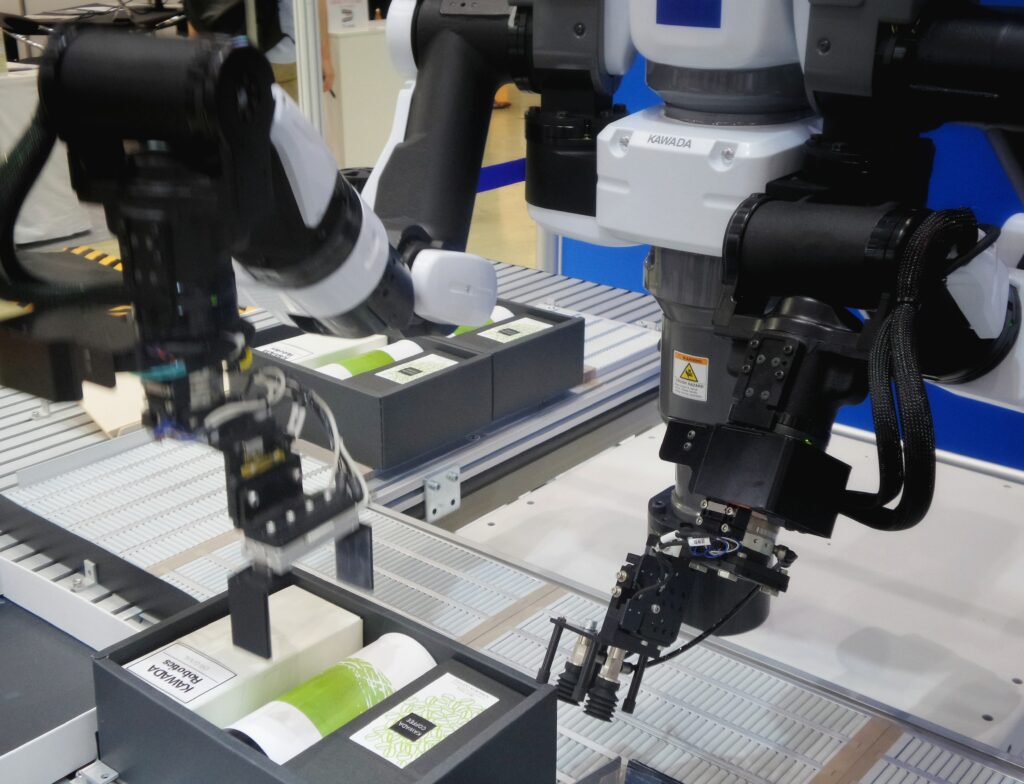
Made From Aircraft-Grade Aluminum Is a Marketing Phrase to be Wary of
I laugh every time I see the claim of using aircraft-grade aluminum in an audiophile or other enthusiast advertisement. Remember when microfiber was touted as this new wonder material? Clothing was being produced with this new miracle fiber. And in many cases, the clothing cost more. Well, it didn’t take long for savvy consumers to figure out that microfiber is nothing more than 100 percent polyester.
Aluminum parts are made from an aluminum alloy. Alloys are a variety of elements mixed together to achieve certain mechanical properties: 6061 and 6063 are two popular alloys used in CNC-machining operations. There are, of course, many different alloys used for specific applications. If the part is made from an extrusion, like the internal frame used by several speaker manufacturers, a temper or artificial aging spec must also be applied. T6 is a very common temper spec. So the engineer specifying a material from which an extruded part will be made would chose 6063-T6 as the alloy to use. This alloy will achieve certain mechanical properties like strength, shore hardness, elongation, and so on.
Aircraft-grade aluminum is to aluminum parts what microfiber is to clothing. It is nothing more than a marketing term, one that is intended to impress you with a perceived level of quality. In truth, it means very little. If an engineer designed an aluminum part used in an aviation application and, on the part drawing, specified “aircraft-grade aluminum” as the required material, the supplier making the part would have no clue how to proceed. They would call the customer and ask the engineer to specify which specific material.
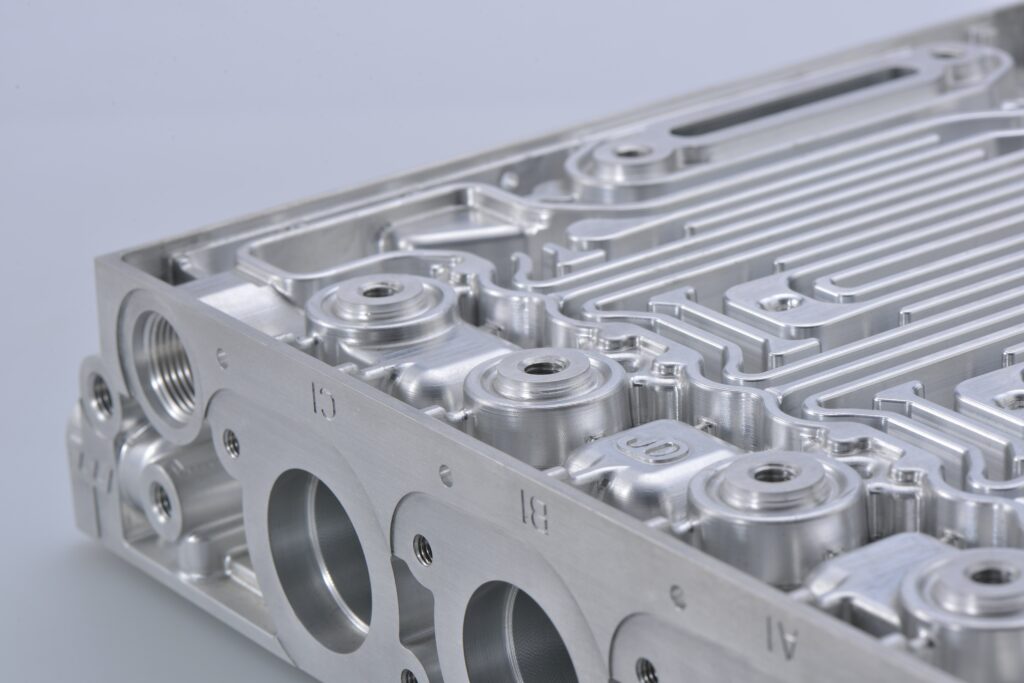
What Other Processes Can Impact Audiophile Manufacturing?
An alternative to machined parts, fabricated sheet metal is also very popular in audio applications. It’s quite common for a component manufacturer to specify a machined front faceplate and use sheet metal for the rest of the box or housing. For audio applications, a laser jet device will cut the part out in lay-flat form from a sheet of metal. It will then need to be bent, which usually takes place on a press brake. There are, of course, secondary processes used to attach fasteners so that one part may be bolted to another, such as attaching an amp’s side panels and top and bottom plates to a machined front faceplate. Fabricated aluminum is substantially less expensive than machining, so it may easily yield a more competitive cost for the component. It should be noted that more expensive equipment will usually not use sheet metal for the outside of the component because, well, a heavy-walled, machined housing looks more expensive and robust…and it usually is.
Molded plastic would be an ideal process to use for audio equipment were it not for two major problems: tooling costs and public perception. There are several different molding technologies, but for space reasons let’s look specifically at injection molding. This is where plastic resin is melted and injected into a mold, which is then cooled (usually by chilled water). Once the hot, liquid plastic hits the chilled mold, it solidifies, the mold opens, an ejector pushes the part out, and it’s finished. The whole process usually takes only a few seconds.
Labor burden is also applied to injection molding. But with process times in the seconds—versus minutes for machining (sometimes 10 minutes or more)—plastic molding yields a much more affordable part cost. But here’s the rub: tooling. The tooling required to make injection-molded parts is usually steel. These machines exert tremendous pressure on the tools, and softer metals like aluminum don’t hold up very well or last very long. Tooling, regardless of the metal used, is quite expensive. Tooling costs can range from $10,000 to $100,000 or more. The tooling costs are amortized into the part cost and are paid by the customer, not the molding supplier. No molding can take place without tooling, and the exact same tooling is needed whether the volume is 10 pieces or 1,000,000 pieces.
Another problem with injection molding, and molded plastics in general, is volume. Molding with plastics is designed for high volume. Part quantities in the hundreds of thousands and up into the millions is not uncommon. Low-volume applications, like most audio equipment, simply don’t bear out economically because as part volume decreases, part cost increases.
One workaround is 3D printing. This process takes a material (and the availability of materials has dramatically improved over the last few years) and builds up the part, layer by layer. It is a very slow process compared to injection molding and is substantially more expensive. It can, however, be used for low-volume applications and requires no tooling. Several manufacturers of higher-end audiophile turntables are using 3D printing to make tonearms. 3D printing sounds very space-age, but keep in mind this is process typically lacks the strength and hardness that injection molding provides. I have some 3D-printed cable elevators that look really cool—but step on one or barely twist it, and it will easily break. 3D printing definitely has some limitations.
Lastly, there is the problem of consumer perception. People will commonly make the judgment that molded plastics are cheap and will break easily. And in the high-performance audio industry, perception can be quite important. Because equipment costs are so high, the gear needs to look expensive if it’s going to be expensive. So machined aluminum is most commonly used.
There are clever alternatives used in other consumer categories. If your car has nice, shiny buttons to roll the windows up and down, guess what—those buttons are very likely not metal. It’s far more than likely that the buttons and almost any bright-looking parts inside your car are molded plastic with a process called Vacuum Metalizing applied. Also called vacuum deposition, a light coating of metal is applied to the plastic part. The end result looks nice and shiny and resembles a metal part.
Could this process be used in an audio application? You betcha. But vacuum metalizing requires its own tooling and is also designed for high volumes. Add that to the tooling costs of the injection-molded part itself, and molded plastics just don’t work for low-volume, highly decorated applications like audio equipment. Which brings us right back to machined and fabricated metals.
Audiophiles take pride in their systems. But the idea of impressing people with system complexities and marketing hype might need to change in the coming years as the hobby evolves. Prices haven’t gone down very often in the audiophile world, and something has to change. Perhaps modernizing some of the manufacturing processes could help bring the hobby to more people.
You did your homework. Well written and accurate article.
Thank you for your kind words.
We are banking LOTS of unique content for the coming months be it high performance gear and new feature news articles that talk about what the traditionalists won’t.
We need the BS out of the hobby. Focus more on how to get the most from your music. I think… 🙂
Thanks Jack,
Very much appreciate the compliment!
Paul
Paul, you must be an industry insider in the metalworking industry. I used to be a buyer in a machine shop (a little-known fact) and I became familiar with metal, machining, finishing, heat treating, anodizing, magnetic particle inspection and all that other stuff. It’s common, as we know, for people to criticize audio components as being too expensive, but sometimes, they ARE in fact expensive to make.
Now you’re making me nostalgic for the days when I use to buy 6061-T6 aluminum, Inconel, 440 stainless and other metals. I wonder what beryllium copper costs these days…
Frank, my “Day Job” is it were, is selling various metal and plastic processes. Basically, I’m a self employed Manufacturer’s Rep. Been doing so since 1988. In metals, I’ve sold fabricated sheet metals, stampings, die castings, sand castings, permanent mold castings, powdered metals, and springs. In plastics, I’ve sold injection molding, vacuum forming (including twin sheet molding), blow molding, RIM molding and rotational molding. I actually worked on a large project for a real fighter jet and I can tell you, those engineers are so specific as to materials, to have one of them release a part drawing with a material call out for “Aircraft Grade Aluminum” would probably get them fired. But we all love to love marketing terms. That they have little to do with reality doesn’t make a lot of difference.
As to beryllium copper, probably a whole lot!!!
Thanks for the comment!!
Hope to see you at Axpona…
Paul