Powered by tremendous enthusiasm from often younger generations, much greater scrutiny is being paid these days to the environment and the impact we have on it. We are moving towards the goal of reducing our carbon footprint. We are looking to reduce or even eliminate the use of fossil fuels from our everyday lives in any number of creative ways. Nearly every automaker is working to replace internal combustion engines in cars with battery powered versions. Chemical companies as well as manufacturers are searching for realistic alternatives to plastics in the form of environmentally friendly replacements. These are all noble causes, to be sure.
What about vinyl LPs loved by many audiophiles and music lovers? They’re made from plastic, right? As someone who made their living in the plastics, chemical, and even vinyl product business, I’ve got a unique insight to the topic of how green vinyl is (or isn’t).
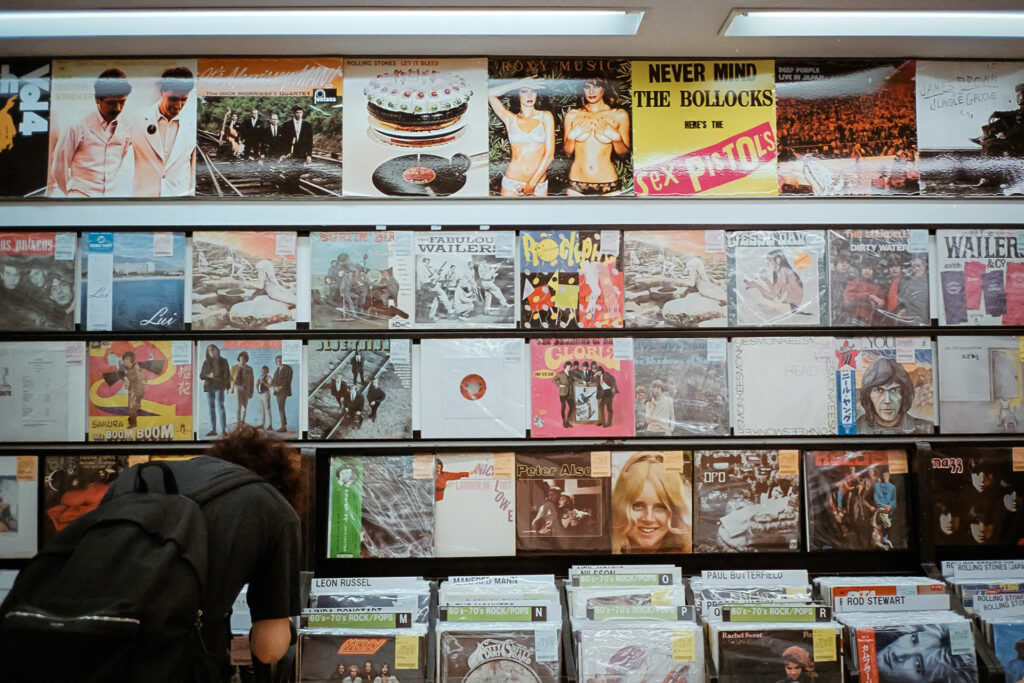
LPs Are Made from Polyvinyl Chloride, a Widely Used Plastic Material
So, what is polyvinyl chloride, or PVC as it is commonly called? And where is it used? PVC is a petrochemical product. Most commonly, it is a derivative of natural gas, or more specifically, gas is refined as one of the first steps in manufacturing PVC. Very briefly, ethylene and chlorine are combined with a vinyl chloride monomer. Then heat stabilizers, often some form of tin or lead, are added, as are plasticizers and colorants. The final product is a resin, or very small pellets that may be shipped in bulk, most commonly in rail cars. PVC resin is also shipped in gaylord boxes and even large bags. Shipping by rail is the most economical and widely used method of transport in most cases.
What Are Some Common Applications for PVC?
Like any plastic resin, PVC may be processed in various manufacturing formats. It may be extruded, like plastic piping for plumbing and electrical applications in the construction industry. PVC is a popular insulation material for wire and cable, again, mostly used in construction – think the electrical wire in your walls. PVC is widely used in the furniture industry for everything from edge-banding on tables and chairs to shower curtains. It is very widely used in the manufacture of profile extrusions for applications such as gaskets and seals on refrigerators, for instance, decorative trim on vending equipment, marine and boating applications, material handling, medical equipment, and yes, even our humble LP. Basically, PVC is one of the most commonly used plastic materials on Earth.
Why Are Vinyl LPs Made from PVC?
PVC is an excellent material choice for making an LP. In most other applications, once a plastic part is made, little else will happen to cause it to degrade or fail. Not so with an LP. While PVC is very stable once processed, an LP is not the hardest substance in the world of plastics. Add to that the fact that a diamond stylus – diamond being one of the hardest substances on Earth – is going to be repeatedly making contact with the much softer PVC surface of an LP. In fact, the circular motion of a turntable platter causes the stylus to exert pressure on the outer groove walls of the LP, increasing the chances of failure. This is why very precise setup of a turntable is so important.
To combat this, PVC has a 10- to 20-percent crystalline structure that helps when molding grooves on the LPs surface. It also aids in effecting repeated use of the stylus tracking through those grooves. Equally important, PVC as a material is usually considered to produce much better sonics than other plastic resins. PVC is therefore a natural choice for an LP.
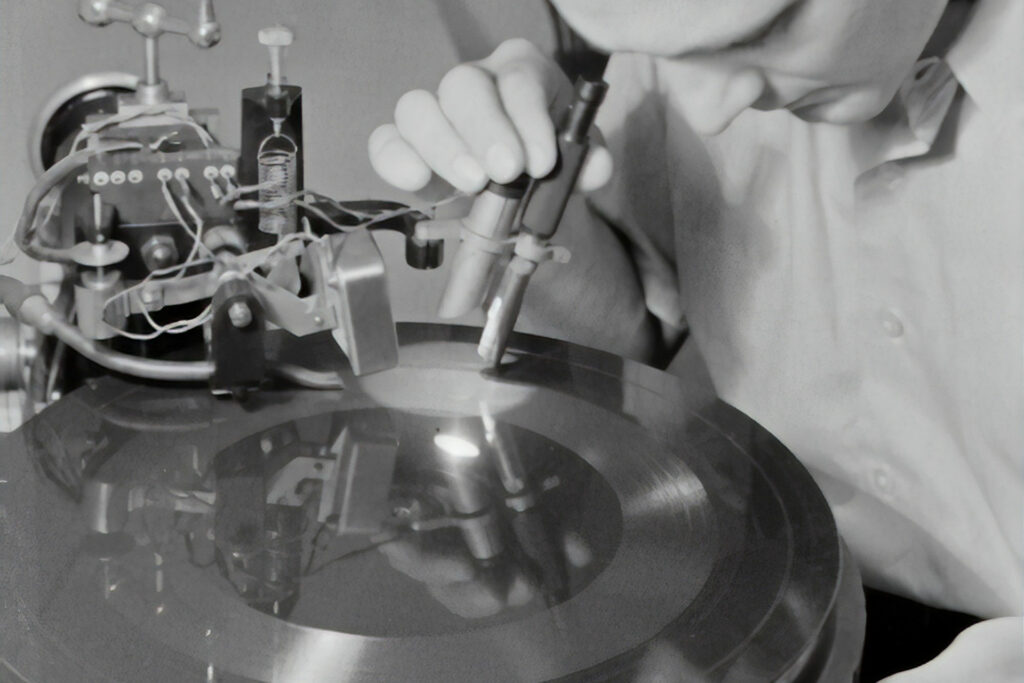
How Is an Audiophile LP Made?
For space purposes, I will be somewhat brief here. For more information on how LPs are made, an Internet search will yield a wealth of information. So, step one is the creation of a master disc. A flat disc is made from an aluminum core covered with a smooth nitrocellulose lacquer. It is also at this point a center hole is punched into the master. As the recording is played, a lathe simultaneously cuts the grooves into the master. A separate master is made for both the A and B sides of the LP.
Now called a stamper, the disc is plated. This process involves spraying the metal disc with tin chloride and then silver. Next it is electroplated – done by dipping the disc into a tank of liquid nickel. An electrical charge permanently bonds the nickel to the silver on the disc.
Next comes the molding process. Both stampers, representing each side of the LP, are loaded into the molding machine. A round mass of PVC, typically called a biscuit (the names vary), is placed into the molding machine. Using about 100 tons of clamping force, or the amount of pressure the machine exerts when closed, both sides of the LP are concurrently formed. The grooves on the stamper are imprinted on the PVC biscuit. The label is also applied at this time. Once the mold opens, the excess PVC is trimmed away, the LP is packaged and is then ready for shipment to you.
What Is the Big Deal with 180 Gram Vinyl Records?
One downside of LPs is warpage. High-end audio turntables with center weights, outer periphery rings, and – on expensive models – vacuum hold down systems, are used to ensure LP flatness. It is always recommended to store LPs standing up, not lying flat on their side. Because all plastics are influenced by heat, it is recommended to not store them in hot environments. Transporting an LP flat in a hot car in the middle of summer is almost guaranteed to warp your favorite record. A normal LP weighs somewhere between 120 and 160 grams. This lighter weight and thinner surface thickness makes a normal LP more susceptible to warpage and deformation. An LP made with 180-gram vinyl is less prone (although not immune) to warpage due to additional mass.
Unfortunately, 180-gram LPs do not offer any real sonic advantages based on material weight alone. They will tend to last slightly longer, again due to additional mass. And some will claim they are more stable on the turntable and will be less prone to slippage. For an LP purist, because 180-gram records have a thicker surface dimension, the stylus rake angle should be adjusted as opposed to the setting for a standard LP. In a perfect world, the angle of the stylus to the record surface should be 92 degrees. If that is achieved with a standard LP, playing a 180-gram variant will alter the tracking angle and, theoretically, the sonics.
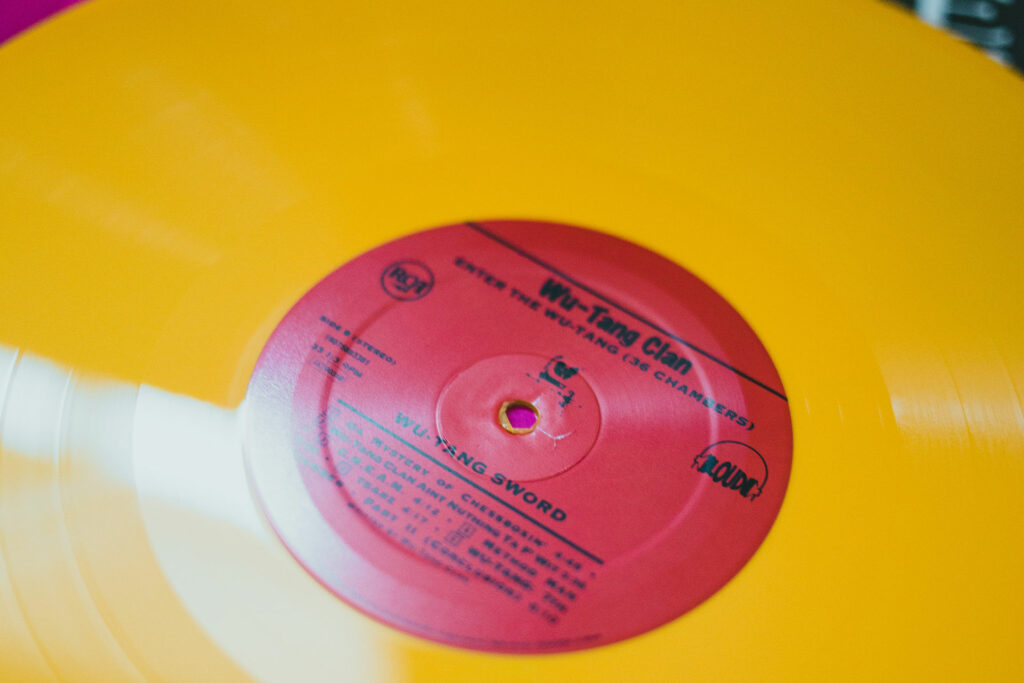
Is PVC Environmentally Friendly?
The short answer is no. PVC cannot be recycled. It is also quite harmful if burned. In fact, burning PVC releases extremely toxic vapors into the atmosphere. More specifically, the chloride gas released when PVC is ignited is a carcinogen. While PVC obviously finds its way into landfills, the time it takes for it to break down may easily be 100 years or more. There is speculation the complete breakdown of PVC in a landfill may take as much as 1,000 years.
What Dangers Are Posed by the Handling and Use of an LP?
If what you have read so far gives you pause, don’t worry. Normal use of an LP is quite harmless. Once formed, a PVC record is very, very stable. Any off-gasses, if they even exist at all, are so negligible most experts agree health risks are not a concern. That said, it is recommended to handle an LP from the edge, not gripping it on its flat surfaces. An ancillary benefit to this is the surface of the LP will not become contaminated with the oils from your fingers which may lead to compromised sonics.
Any dangers resulting from an LP are almost the exclusive province of the manufacturing process. When molded, the pressure and heat necessary to form the PVC biscuit into a finished LP may cause a small amount of toxic smoke or vapor to be expelled. This potentially affects the workers in direct proximity to the forming equipment and not really anyone else. Record-pressing plants typically take preventative measures to evacuate these vapors, thus keeping worker safe. Anyone who enjoys the sound of an LP need not worry about personal safety. Unless, of course, you plan to set your LP collection on fire while standing by breathing the fumes. And given what LPs cost, who would do that?
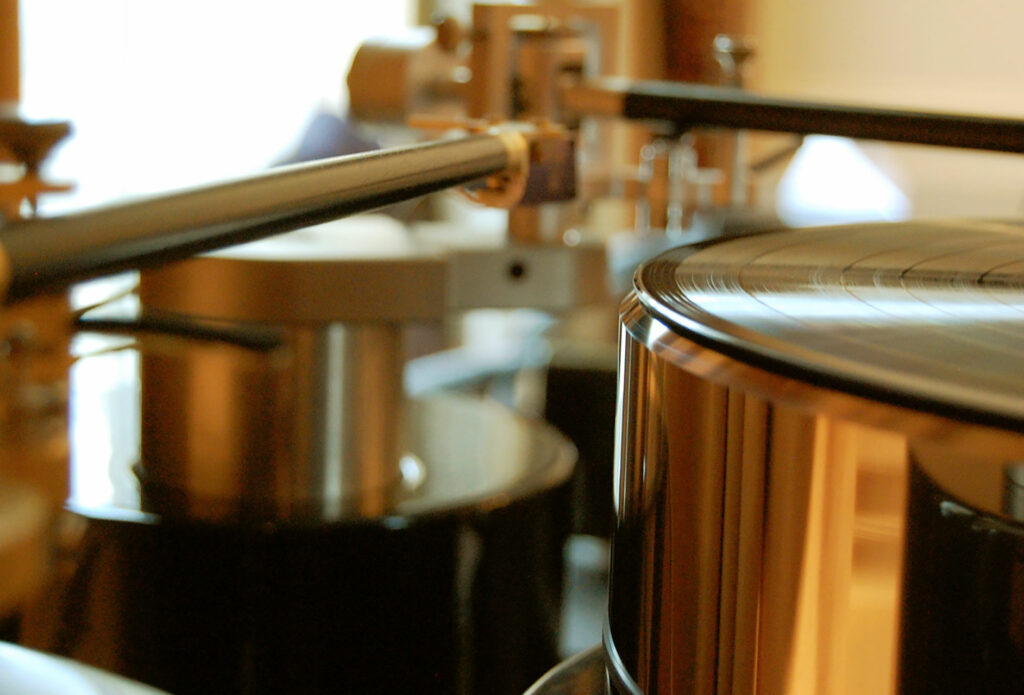
Are There Any Green Alternatives to PVC LPs?
As a matter of fact, there is increasing attention being paid to this very issue. There are two companies who seem to be leading the charge, both of whichclaim environmental advantages over the tradition method, although their approaches are quite different.
Green Vinyl Records, a consolidation of eight Dutch companies, is working to improve the environmental footprint of LPs and also reduce cost. Their approach is to re-engineer plastic materials and employ more automated molding processes. Chief among their process is eliminating the slow, labor-intensive compression molded process used for about 100 years now, and replace it with nearly fully automated injection molding production lines. They also claim to have formulated more environmentally friendly plastic resins than the current PVC resins so commonly used today. While they claim to replace toxic materials with environmentally friendly variants, I did not see a breakdown of what those materials actually were. And there is the issue of pressing plants scrapping the compression molding machines used in LP production and replacing them with very expensive injection molding machines. How well this catches on with existing pressing plants the world over remains to be seen.
Another company in the forefront of a reduced carbon footprint is a UK-based company called Evolution Music. They claim to have replaced traditional PVC based resins with what they call Evovinyl, which is a plant-based material. In trials conducted at a variety of pressing plants, the same equipment is used as when making LPs from PVC. What changes are reduced forming temperatures, which is claimed to provide lower energy consumption. Because the material itself is “bio” based, Evolution Music asserts environmental neutrality. They additionally purport the sonics are indistinguishable from the PVC records they hope to replace.
Not much is given in the way of what comprises the actual material or any measure of technical information. However, it is felt by many in the industry this alleged environmentally friendly material will one day replace PVC because of the elimination of toxic off-gasses. Not to mention pressing companies being able to use their existing equipment seems to provide a viable alternative to carcinogen-producing materials like PVC.
Nor do we know how much records produced using this process will cost. I am reminded of when diet foods first began showing up in stores. When “diet” appeared on the label, it usually meant higher cost and worse taste. It remains to be seen if something similar will happen with a bio material for LPs.
Conclusion
LPs are a beloved format by not just old-school audiophiles but also by many other music enthusiasts as well. Millennials, Gen Xers, and, realistically, all age groups enjoy listening to LPs. There is a magical quality to the tactile application of a stylus touching a record. Listening while holding an LP sleeve and reading the who, what, and where of a proudction adds to the overall satisfaction and enjoyment of the format. And who can discount the sonic quality an LP provides, most notably a warmer, more relaxed sound as compared to a CD?
As our world struggles to pay greater attention to carbon footprints and keeping the Earth clean while still enjoying modern conveniences, there will undoubtedly need to be sweeping changes to traditional norms. While LPs made from toxic, even cancer-producing materials like PVC are considered by many in need of elimination, there is not yet a leader in the race to create a dominant replacement. I suspect PVC will continue to be the go-to material for a cost effective, sonically superior material for an LP. What supersedes it, and when, is as yet a question in search of an answer. How soon answers are reached remains to be seen. Meanwhile, enjoy the records that you have and will buy in the coming years. I know I will.
A great read Paul! I’m sure like many things the largest barrier will be economics. If places like Third Man Records (the current largest producer of LP’s globally) can make the change without a large negative change to revenue then we will see it happen. Otherwise, we will have to wait on other pressures.
I heard that Mobile Fidelity is opening a pressing plant in Los Angeles despite the controversy over using DSD for their masters (a fine practice but they shouldn’t have lied) which will help get more volume into the market.
Many think that supply is the key issue in the high cost of vinyl these days. Simply put, there just isn’t enough to meet demand right now.
Many thanks Andrew, I’m happy you enjoyed the piece. This one was fun to do and I found it interesting that these two companies are investing so heavily to replace PVC for LP’s. How well they do so remains to be seen! I wouldn’t expect anyone to pay two to three times more for a non vinyl LP than a PVC version no matter what claims about being carbon neutral are made. As it always does, it boils down to material and processing costs. Or as you so correctly stated, economics.
Take Care!
P
I am awaiting part 2, where you can compare the results of these new materials. Nice article.
Paul may do that later, down the road…
Say hi to Pierce for me.
I would LOVE to do a comparison of both technologies to vinyl. Based on what I discovered about either company, things are very much in the preliminary stage. Not sure how soon anything will be commercially available. But when they are…
Thanks for the compliment Brad, much appreciated!
P